Labels
New Sensor Could Prolong the Lifespan of High-Temperature Engines
A new, highly-accurate temperature sensor could save manufacturers millions in maintenance costs, lower fuel consumption, and prolong the lifespan of jet engines, nuclear reactors and other types of large gas turbine engines.
A temperature sensor developed by researchers at the University of Cambridge could improve the efficiency, control and safety of high-temperature engines. The sensor minimises drift -degradation of the sensor which results in faulty temperature readings and reduces the longevity of engine components.
The new sensor, or thermocouple, has been shown to reduce drift by 80 per cent at temperatures of 1200 degrees Celsius, and by 90 per cent at 1300 degrees Celsius, potentially doubling the lifespan of engine components. The results are published in the September issue of the Journal of Engineering for Gas Turbines and Power.
Generally, the hotter a jet engine burns, the more power it generates, improving fuel efficiency, range and thrust. However, an accurate temperature reading is critical, as when temperatures get too high, the mechanical integrity of engine components could be at risk. A temperature error of just ten degrees can trigger engine failure, which can be a huge blow to aircraft manufacturers, as seen in the 2010 recall of Rolls-Royce's Airbus A380 engines, which caused the company's share price to drop by a massive nine per cent.
Modern jet engines can reach temperatures as high as 1500 degrees, but drift in the nickel-based thermocouples used to measure temperature increases to unacceptable levels at temperatures above 1000 degrees. Therefore, the thermocouple is placed away from the hottest part of the engine, and the maximum temperature is extrapolated from that point.
The inaccuracy resulting from this form of measurement means that the engine temperature, and therefore efficiency, has to be set below maximum in order to leave a safety margin for the survival of engine components. Thermocouples with increased temperature capabilities can be placed closer to the combustion chamber, increasing the accuracy with which the peak temperature is estimated, and decreasing the required safety margin.
"A more stable temperature sensor provides several advantages -- a better estimation of temperature can increase the lifetime of engine components and decrease maintenance costs to manufacturers, without any reduction in safety," said Dr Michele Scervini, a postdoctoral researcher in the Department of Materials Science and Metallurgy, who developed the new thermocouple.
In its simplest form, a thermocouple consists of two bare wires of two different metals joined together at their ends, with a voltmeter incorporated into the circuit. The difference between the two ends of the thermocouple is measured by the voltmeter and used to determine the temperature. This type of thermocouple is not suitable for high-temperature applications as the elements oxidise above 800 degrees, increasing the amount of drift, so thermocouples sheathed in oxidation-resistant materials were introduced in the 1970s. While this configuration addressed the issue of oxidation, the sheath contaminated the wires at temperatures above 1000 degrees, increasing drift.
Scervini, along with Dr Cathie Rae, has developed a thermocouple which both withstands oxidisation and minimises any contamination to the wires from the metallic sheath. The thermocouple is made of an outer wall of a conventional oxidisation-resistant nickel alloy which can withstand high temperatures, and an inner wall of a different, impurity-free nickel alloy which prevents contamination while reducing drift.
Results from tests on a prototype device showed a significant reduction in drift at temperatures of 1200 and 1300 degrees, meaning that a double-walled thermocouple can be used at temperatures well above the current limitation of 1000 degrees.
There are platinum-based thermocouples which can withstand higher temperatures, but their extremely high cost means that they are not widely used. "Nickel is an ideal material for these applications as it is a good compromise between cost and performance, but there is a gap in the market for applications above 1000 degrees," said Scervini. "We believe our device could see widespread usage across a range of industries."
The team are currently commercialising their invention with the assistance of Cambridge Enterprise, the University's commercialisation arm, and have attracted interest from a range of industries. Tests on new prototypes are on-going.
Taking Turbulence detection to the next level
Those of us ho have ever flown past or to mountainous destinations or regions can hopefully smile as they read through this article…even though some will be disappointed because it is not yet in their country. Still, if you have had your flight diverted to some town you did not like going to due to turbulence then just hold on for this. Here I Kenya, I advise the KCAA and KAA to work together and bring this system to JKIA-though it is not that prone to turbulence anyway.
What is this I am blowing trumpets and vuvuzela’s about all around without explaining just what it is? I am talking about an advanced airport system developed by the National Center for Atmospheric Research(NCAR) and installed at Juneau in July 2012. I heard about it in TWIE episode 121 where I liked the way Vince Penman presented the system. I then followed it up and read more about it here. It provides information that pilots can use to control aircraft to evade catastrophic turbulent spots. It is based on a network of instruments and computational algorithms to analyze the ever-precarious atmospheric parameters.
The system was launched at Alaska’s Juneau International Airport and research is on to tailor-modify the system for use at other airport hit by turbulent at frequent intervals e.g airports in Northern California and the Mountain West to New Zealand and Norway. The predecessor to this system is a similar one designed by the same company and used at Hong Kong’s Chek Lap Kok Airport.
At the Alaskan Airport, it is known as the Juneau Airport Wind System(JAWS). The system has not only reduced flight delays but has literally almost done away with the turbulence risk of flying into and out of Juneau. One of the scenarios is when there is a lot of turbulence and it simply highlights a nice path for landing and take off.
Something else I learnt was that the system did not just come to pimp up the airport. There was a time when turbulence has led to closure of this airport at some times when it is so risky to come in or go out. But then, this was not the best way to do things when we know that the only way out of this place was by airplane or boats. This necessitated that the problem be surmounted by all means. The NCAR team that worked on this used research aircraft and computer simulations to investigate the different wind patterns and effects of glacier in addition to anemometers and wind profilers that really help accumulate a lot of data for this project.
Additive manufacturing
When you refer to disruptive technology-a type of technology that disrupts the normal day to day operations, meaning it is unique in such a way that manufacturers need to get used to it in a major way-though the package includes advantages in expenses, time and efficiency. Many people, just like the Director of GE Aviation does, think of additive manufacturing as some kind of disruptive technology.
Power-bed additive technology builds up parts by stratification and bonding (using concentrated heat sources like electron beams or lasers) of layers on top of each other, forming cross sections of the part in 20-80 micron thicknesses. The outcome of the process can be very complex parts that cannot be produced using the commonplace methods. It can also combine and put together items from traditional manufacturing processes to form intricate mechanisms. Most of the hackneyed manufacturing processes build components with multiple steps or need multiple parts brazed together while additive manufacturing allows one to combine these into one big step. This means the complex parts can be optimized for weight and strength to serve different critical applications.
Additive manufacturing, though still an immature field as of today, shows signs of exponential growth. This growth seems to be going hand in hand with propping technologies like software and computing. Industrial players also expect an increase in the size of parts that can be manufactured.
Quality assurance for Composite materials
As an increasing trend, the use of composite materials has faced various challenges. The most underscored challenge that I could point out is that of ensuring quality assurance. A light-weight design of carbon-reinforced plastic (CFRP) utilizes adhesive bonding as the optimum joining technique but quality monitoring procedures are still an issue but once that is circumvented, it will provide a basis for increased use of light weight composite materials for more structures reducing the dominance of rivet based assemblies.
The admirable properties of adhesive bonds are significantly depended on physicochemical behavior of adherend surfaces. This implies there is need for a set of highly advanced NDT techniques to counter check the resulting products of the ENCOMB (Extended Non-Destructive Testing of Composite bonds) project. Adhesive bonding, which we even learnt about in High School, has been established in the Aeronautics industry for more than 20 years. Currently, however, it is mainly used for non load critical parts or components like stiffness panels of vertical tail planes. So, to explore the full potential of this joining technology as applied to other load critical parts like the frame floor modules or fuselage structures, we need adequate Quality assurance procedures. QA procedures for the members that are not load critical are present-conventional NDT to detect defects like pores in the joint areas. As an addendum, the supplied materials (adhesives, prepreg materials) and parameters of the manufacturing processes (like surface treatment and curing) are strictly observed and controlled. It has been established that the overall performance of adhesive bonded CFRP components depends on the intensity of operational loads and the size and density of defects like pores. The adhesion is highly vulnerable to state of the adherend surfaces (for instance degree of contamination and activation after surface pretreatment).
I would also like to bring you to the attention of the two main objectives of the ENCOMB project.One is the development and adaptation of methods of characterization of adherent surfaces before application of adhesive. The second and harder one is the development of techniques for the evaluation of the bonded components resulting from the process. This new approach to testing, referred to as the Extended NDT (ENDT) is based on detection of physicochemical properties that are important for the performance of an adhesive bond. Some ENDT methods are adapted from the spectroscopic methods like IR spectroscopy or Laser Induced Breakdown Spectroscopy (LIBS), and optical methods like laser scanning vibrometry, active thermography and a wetting test. All these help to categorize the state of adherend surfaces. Sensor/fiber based methods like use of embedded optical fiber sensors (EOFS) or electrochemical impedance spectroscopy (EIS) are also suitable for monitoring characteristics of adherend surfaces and adhesives. But mostly for characterization of adhesive bonds, technologies from the field of active thermography using variant excitation sources or optical coherence tomography are applied. Elastic waves techniques like laser excited ultrasonic techniques or nonlinear ultrasonic techniques will also be considered.
Two outstanding contenders
Normally a liquid drop is applied to a surface during the testing and the size of the drop mainly depends on the surface energy and the corresponding contact angle. For the Aerosol Wetting Technique (AWT), small water droplets with a narrow drop size distribution are generated by an ultrasonic atomizer nozzle and sprayed onto the sample surface by a constant airflow. A camera positioned perpendicular to the surface takes a photo of the wetted area. The drop sizes are grouped using software and the mean drop diameter is determined by a two parameter fit to a Rosin-Rammler drop-size distribution. A large mean drop size shows a good wetting property and high surface energy. If the surface energy is low and this is normally caused by surface contaminants like silicones or Teflon, relatively small drops will be formed on the surface hence a small mean drop size. The AWT process is very surface sensitive and can detect surface contaminants (Frekote/Tedlar) on CFRP surfaces and the effects of different plasma treatments that have an influence on the fracture toughness energies of corresponding bonded samples. The accuracy and sensitivity of the measured results can be ameliorated by further statistical analysis, image acquisition and evaluation for droplets on dark and low reflecting CFRP surfaces. The suitableness of the AWT for other scenarios like detection of Skydrol contaminants on CFRP is also something to be looked at.
The Laser Adhesion Test (LASAT)
This method is based on inducing controlled traction by irradiating the target with a high power laser pulse (GW/cm2). The laser energy excites high power plasma (GPa) at the surfaces. Thus, a mechanical shock wave is induced inside the target. The LASAT technique relies on the crossing of two releases that are generating traction. The first release is due to reflection of the incident shock wave at the rear free surface. The second one follows this incident shock wave since the maximum pressure is brought back to the ambient pressure at the end of the load duration. In this way, interface could be damaged if the level of tensile stress exceeds the bond strength and if the shock waves propagation parameters (shock duration and amplitude, materials nature and thicknesses) allow locating the release crossing at the interface. Damage can be assessed by post shock diagnostics (like ultrasonic testing, microscopy) since the shortness of laser impact allows a soft recovery of shocked samples. It can also be done by measurement of rear free surface velocity (velocity interferometric system for any reflector or heterodyne probe). This nonintrusive diagnostic provides clear evidence of the debonding or integrity by very different velocity time histories. Coupled with numerical simulation of shock wave propagation and damage modeling, experiments give a quantitative evaluation of the adhesion threshold of coatings. So use of lase shock waves applied to CFRP bonded samples has shown its ability to differentiate strengths of adhesion. There is more to be learnt on shock wave propagation into CFRPs and adhesives in order to optimize laser parameters to induce a controlled traction at the interface of a given system.
Ref:
Article in SAE Aerospace engineering issue of 15th August 2012
SAE technical paper 2011-01-2514 by Susanne
Goodrich Corp’s GA64OC-15A shortwave infrared camera (SWIR)
The Goodrich Corp’s GA64OC-15A shortwave infrared camera (SWIR), compared to other IR cameras in the same category of functionality, is actually much smaller, weighs less and utilizes low amounts of power than others. It weighs about 26g without the lens and is the right choice for integration into handheld, helmet or weapon mounted surveillance devices, unmanned aircraft and any other imaging system where minimal size, weight or power consumption are vital parameters . It has a resolution of 640x512 pixels with a 15-µm pitch. You can find much more about it here.
You can compare it with other cameras here.
What about internet during our flight?
Rarely do we concentrate on entertainment as a major part of the Avionics in an aircraft. Just until recently, when global trends force us into it. Nowadays, portable computers, can be tablets, laptops or whatever have become the norm and this has been observed as a way of attracting customers. What am I saying…you may wonder-it has been observed that airlines are trying their best to claim their market share by providing passenger with something special, internet connection.
Many aircraft today, both private and commercial have antennae than communicate with satellites or towers that help access the internet. Even though most of the equipment are towers(on the ground), satellite sources have recently been hugely adopted and these increase in use has pushed their prices lower enough for more affordability. From an article I read in the SAE Aerospace engineering issue of 15th August 2012, In-Stat predicts that by 2015, 6100 commercial planes will have internet access-3 times the number that had last year(2011). In USA for example, Gogo has been doing the tower thing which has been nice and reliable domestically but airlines go past country boundaries hence the need for satellite services. Comparatively, Satellite services are more expensive, but again it is not pragmatic for many aircraft to carry both types of antennas-the drag caused will be too high. Also, Air-To-Ground (ATG) networks are time consuming to set up.
This obliges airlines to pick one connection, as does not sound politic to have both, neither is it better to bounce between ATG’s and satellite connections. Another issue is that though satellite connections seem a viable solution, an aircraft on a trans-continental or trans-ocean trips will not be able to track one satellite all through. It needs to connect to at least three of them and the switching is not as easy as a cell phone switching between towers as one travels in a car. There is need for attention to some minute details (like Doppler compensation depending on speed) for a successful re-orientation and precise focus on another satellite to facilitate a continuous connection. Another pothole to look out for is to ensure that satellite communication does not overshadow the link between the air traffic controllers and the pilots.
So far, most of the links to satellites use Ku-band, a well-established technology-though many are anticipating the Ka-band links that will have a larger bandwidth.
The other challenge is a design one, because many passengers will be accessing the internet and doing may be 4-5 things, facebooking, listening to music, watching a movie…you see. You can imagine most of the passengers using the internet and the situation is not the same as that in a local cyber café because in an aircraft there are power consumption and weight that we will be adding just by adding few more routers to make the internet connectivity more efficient. Also, it won’t be a good idea if passengers have to wait every time the system is switching from one satellite link to another.
This calls for a very good Real Time Operating System (RTOS). Bombardier, working hand to hand with satellite provider Inmarsat, is among the companies that have surmounted all these challenges and established a very nice internet access system.
Something is missing….Bird strike kills all!
My euphoria about the engine that could not succumb to bird strikes never stayed that long…really. I had thought we just found an answer to seal away all these gruesome conditions where a bird imagines to be flying into an advanced nest only to end up in double tragedy-deaths and a damaged engine! Anyway, this happened before someone could implement this in a real aircraft.
This happened on 28th September 2012. The Dornier Do-228 owned by Sita Air climbed up the runway from Kathmandu, Nepal headed to Lukla-still in Nepal. It had 3 crew members and 16 tourists on board and was right in the beginning of that first climb up the runway when a bird accidentally flew into the engine and damaged it. As usual, the first course of action is to return to the airport and land but, in this specific case, this did not work as the aircraft descended at a very fast rate and could not make it to the airport. The only other option was to land at the bank of Manohara River, Koteshwor village. However, this again, did not end well as the plane crashed on that river bank and went up in flames completely consuming everybody and everything…so doleful an end.
According to investigations, a bird hit the right hand engine at about 15m above the ground and caused a part of the engine to separate from the engine and disfigure the rudder. This rendred any turn uncordinated hence the move back to the runway uncontrollable as the pilot could no longer maintain ascendancy over the plane for longer.
To view some more information, you can check here. Some of the pictures are displayed here.
Top five reasons why Aviation is my way to go
Effect of wind farms on radar signals
The composite fear factor
What are composite materials?
A composite materials is a combination of more than one material put together because each one has a desirable property that we would wish to exploit but we need other properties that are vested in other materials so we join them together and have all the properties we need. Using composite materials also allows the bad property in one material to be ameliorated by the other material that just does better.
If my material science and engineering materials course work serves me right, composites are mainly made up of two components: fibres (fibres to provide tensile strength and flexibility), and a “matrix” to hold the fibres together (providing compressive strength and control of the overall shape).For instance, the “carbon fibre + epoxy resin” combination is widely used in aerospace.
Is it new?
The use of composite materials to build aircraft is not something we can call “A new trend”. It has been around for decades(even before the mid 1980’s) but what we have seen now is a huge increase in the number of parts that are being made with composite materials. In fact in 1988, Airbus introduced the A320 while in 1995, the Boeing Company introduced the Boeing 777-both airplanes in production had all-composite tail sections.Even the DC-9 has parts made of composite materials in it, only that they are few compared to the modern airliners that are being rolled out of factories like the Airbus A350 and the Dreamliner. These aircraft that started offering commercial services after 2011 like the A350 and the Boeing 787 do fly, yes that’s true but being the first generation of aircraft to be mostly composed of parts made of composite materials other than those made of the long safety-trusted metals.this quick transition is something many are deeply questioning despite trusting the work of the engineers and researchers that have worked on it.
The Dreamliner was the first mostly composite aircraft with 50% composite fraction(without the engines) and ferries 210-290 passengers. Next is the Airbus A350, having composite material fraction nearly equal to that in the Boeing 787 but with longer range and higher seating capacity from 250 to 400-plus passengers.
3 – Why did these guys decide to go put in more composite?
Seemingly, we were asleep for all that time only to wake up and find our sleep dream lined….But let us try to understand the truth of the matter because it is not true that long ago, our grand fathers did not realize that composite materials did better. Something imperative to note is that technological breakthroughs in engineering, materials sciences and manufacturing have propagated the notable increase in the use of composites over the past two decades. The use of composite materials has not only invaded aerospace, but also commercial and race car industry, marine industry and the sporting world among many other industries.
Advantages and disadvantages
Composite materials normally result in materials with increased strength, toughness and stiffness. Compared to metals, they have a better strength and stiffness-to-weight ratio. They also boast better corrosion properties and fatigue resistance.This means the planes will last longer and will not require so much maintenance as often. Because of the low weight, there will be lighter aircraft, hence lower fuel consumption and reduced pollution to our environment.
Of course there is no way on earth we will just get all these goodies for free…we must pay something. Setting up a composite production industry is very expensive just say several millions of dollars. Though, over the past decade prices have reduced making composites more accessible and suitable for large-scale aviation projects. Moreover, most manufacturing processes are labor-intensive and high engineering materials knowledge is a necessity. Even the training on composite materials is very expensive making the general manpower package not a very cheap idea to think about.Something else is that we can’t just handle composite materials anyhow….there are handling equipment and specialized storage facilities that are required and this adds more costs, For example, some composites come in “prepreg” form (fibers pre-impregnated with resin) that need frozen storage and have a very limited shelf-life (a few weeks/months).
Then there are issues to do with the safety of workers and staff handling the composites. Several composite material components are classified as hazardous because they have related health issues including complications from inhaling fibers and exposure to suspected carcinogens.
Hurdles to jump
Something else often overlooked by many is the process of commercialization. You don’t just wake up and have your way…there is definitely a process to follow.Before a company is authorized to start manufacturing commercial aircraft, there must be certification and safety assurance procedures first. The US Federal Aviation Administration (FAA) and the European Aviation Safety Agency (EASA) are in charge of investigating aircraft safety and delivering the required certification.
For example, before Boeing started manufacturing the Dreamliner, it was not a question of the many orders already in place for the aircraft but first it had to prove its safety standards to the FAA and EASA.
Lets bring in Robotics now
Lets take an example of a company like Airbus that has received so many order for the Airbus A350 or A380, how do we expect it to deliver 12 aircraft per month all with manual labour? To me, it seems impossible. But if we think about it, we can bring in assistance from robots to make it faster. This will ensure the process is very efficient and will run even during the night, tirelessly. This idea of automation, I remember from a certain magazine, came up in the 1970’s but technology had not developed that much hence it was somehow rendered impracticable as it would be so expensive to implement.
However, in the recent past, low-cost robotic arms have been used for a number of manufacturing processesand Robotic Fibre Placement (RFP) heads started to register their presence more frequently in the market. These placement heads can lay composite materials (using different methods depending on the part at hand) either in a mould or directly on to a desired structure (see video).
B-1 Bomber Targeting pod software for precision
Sometime ago, the U.S Air force advanced 23 million dollars to Boeing to finish the second phase of the B-1 laptop-controlled Targeting Pod software upgrade. The second phase enables the bomber’s targeting pod to find stationary targets and transmit GPS co-ordinates using its avionics system to the weapons- a process that was very manual and used to introduce many errors. It will also complete the integration of the Sniper pod with B-1 programs enable single-moving –target kill capability using laser technology of the Guided Bomb unit.
ESP PC-based visual simulation for better pilot training is also provided to ensure pilots are best equiped with knowledge and practical exposure of the combat missions with less expenses for faster learning.
War fighter pilots stand to highly benefit from this massive resource to hone up their skills in battle. This is after Lockheed Martin and Microsoft Corp. signed a license agreement to continue development of Microsoft’s ESP PC-based visual simulation software platform. Lockheed Martin, now with access to the ESP technology portfolio, will be able to build more economic simulation solutions for customized training of the various customers.
With that in mind, testing and learning has been accelerated in recent times and is nearly done, and may lead to the Air Force's Air Combat Command plans to approve sending pod-equipped bombers on operational missions by mid-summer. With the powerful software, the Pilot in command can easily cross check co-ordinates and visual locations of targets before dropping weapons and would be very profitable for combat for example in places like Iraq and Afghanistan where the B1 Bomber has been used in the past.
Diesel engines in Aircraft-what do you think?
Let us say…we are revisiting this idea, because it is not just out of the woods. This is something that was there many years ago. Let’s take for instance, the late 1930’s when the Junkers built JUMO-the series of 2-stroke diesel engines whose advantage of fuel economy and mechanical efficiency made them very popular. Talking of such a 2-stroke engine, no poppet valves and its junky operating and timing system, no friction losses due to valves –compare this to the 4-stroke engine and you will surely visualize what I am talking about. Again, why fuel? Can you imagine that depending on size and type of aircraft, the largest portion of it is fuel, sometimes can be as high as 50%!
With the 2-stroke diesel engine, it is possible to attain a high power density and fuel efficiency while at the same time enhancing altitude performance. Another salient feature of diesel engines is that it allows a higher boosting level in comparison to spark-ignited(SI) engines whose capabilities are limited by knocking-yet we know that high octane rating fuel like JP4, JP5 and Jet A is now being subject to very strong limitations due to the damage to mother nature. We haven’t exhausted the list of advantages yet; there is the low volatility of diesel compared to other fuels meaning less explosions and fires. It also has better reliability in flight-no mixture control issues, no carburetor icing issues and safe cabin heating due to reduced exposer to carbon monoxide. Let us also not gainsay the fact that the 2-stroke engine cycle has the exemplary ability to maintain a high power density at a very low crankshaft speed, hence can be directly engaged to a propeller shaft even without the reduction gearbox hence cheaper.
These advantages, coupled with the recent developments in the 2-stroke, compression ignition(CI) diesel engine technology make this an auspicious choice for small planes that only need 100-300 hp, at a lower weight than the existing SI engines. This is very pragmatic owing to the trials by AVL in the late 1990’s when they developed a 1-L, 2-stroke turbocharged diesel engine with uniflow scavenging, achieving a brake power of 50kW and a weight less than 80kg. Another proof of possibility is given by Wilksh Airmotive that brought to the experimental aircraft market a 90kW 3-cylinder 2-stroke engine with IDI (indirect injection)-only weighing 100kg.
Generally, we can say that so far, none of the models has reached certification stages as I am writing this article but we are sanguine that more research and trials with several engine configurations will yield expected victory. Some of the selected engine configurations are like the loop and uniflow scavenging type, as opposed to the piston uniflow type.
Research at the University of Modena & Reggio Emilia and Wilksh pointed out that the uniflow type was actually more intricate (would be heavier and more expensive to manufacture) though had flexibility of exhaust timing events via cam-operated valves. On the other hand, though the loop scavenged engine had the trappings of “simple and cheap”, it brought with it symmetrical inlet and exhaust event timing. It also has more to offer in terms of Power-to-Weight ratio, Fuel efficiency, altitude performance and cooling.
For now, at least we leave the rest for research to decide.
This article has been influenced by another article from SAE Aerospace magazine August 2012.
The TaxiBot is here
We are still all about reducing emissions and now at airport level where taxing is another area that huge jets like the Airbus and Boeing use up and burn a lot of fuel while taxing around to a hanger or maintenance bays. This is where we bring on stage one Ricardo who has worked with Israeli Aerospace Industries(IAI) for about 15 months to develop the TaxiBot- a 52-tonne, six wheel pilot operated robotics vehicle without aircraft width, taxiway or airway limits. It could require airport infrastructure changes but will end up reducing noise and air pollution. The structure includes an IAI patented turret, energy absorption systems and controls. The aircraft nose wheel is clamped on to the turret that can tilt,rotate and move axially. The bot has 2-500hp diesel V8 engines a, hydrostatic drive system and a hydraulic system that can handle four wheel steering and aircraft pickup and clamp actuators. It has electronic controllers for force, communication, navigation and speed control.
Its operation is in such a way that, once the bot is engaged with the aircraft nose and locked in place, the turret is able to rotate freely and even take steering and braking commands from the nose wheel directly such that the pilot will not notice that he or she is being towed by a bot. It is however, imperative to learn that aircraft brakes slow down the aircraft and not the tug. At the end of the process, the bot won’t require any driver apart from the pilot in the aircraft. After testing was done, the demo version was shipped to Toulouse airport for further field tests and improvements done before production.
Ricardo’s project that run since 2008 underwent successful testing as seen in the various photos here and the contract has been renewed to allow Ricardo to continue the development of the TaxiBot to the next level. The testing of the first TaxiBot was carried out in 2010, towing an Airbus A340 aircraft at Toulouse airport and subsequently, a Boeing 747 of the Lufthansa fleet at Frankfurt while being maneuvered by the pilots of the respective aircraft. The weather at Frankfurt was not very good but according to IAI reports of this testing, a Lufthansa test pilot was quoted to have really praised its performance on icy and slippery grounds. The second phase of development is expected to see the first commercial implementation of the TaxiBot this year.
Optimizing engines for greener combustion
Well, its not like green is my favorite color…okay. It may be yours but it’s mother’s favorite. Did I just say mother? I meant Mother Earth! Under the social responsibility of corporate institution, is environmental responsibility and since most use already manufactured products, the buck stops with manufacturers in terms of materials and configurations used in component manufacture. However, the information has to be passed to consumers like airlines to ensure that the maintenance is done well to conserve and improve upon the parameters already included.
We know that Carbon (IV) oxide emissions is a function of the quantity of fuel burned. We need to focus more on the combustor where oxygen and fuel are mixed and burned if we have to reduce the noxious emissions that remain close to the ground like NOX, uncombusted hydrocarbons, particulate emissions and aerosols and smoke . To address this, we have to look at injectors, swirlers and atomization of fuel. NASA’s Glenn Research Center has been at the forefront of work on improving injector combustion efficiency. At this center, engineers have been trying several injector configurations and air –mixing methods and have developed the Lean Direct Multi-point Injection (LDMPI).
Among the burning goals has been how to put maximum numbers of injectors in minimum areas to improve combustion-the more completely combusted the fuel, the less the emissions. Multi-point refers to the many different entry points of fuel into the combustor. Regulatory agencies like ICAO have set up stringent rules and standards for pollution that have to be met.
NASA has also gone ahead to burn three different types of fuel in LDMPI testing including two Fischer-Tropsch(F-T) and one biofuel. Although they didn’t really significantly change emission quantities, they solved the issue of clogging in combustors due to tinier injector tips as kerosene is burned. The tests were done at NASA’s Dryden Aircraft Facility and used DC-8 engines both main and auxiliary Power units.
Still, under Environmentally Responsible Aviation(ERA) program, there is a need to reduce cooling air necessary to regulate temperature of metallic combustion liner that can easily melt it if not for the cooling breeze. But then, the less air used for this cooling, the more we can utilize in combustion.
GE Aviation is using the lean/burn combustion to run the GEnx engine that powers the 787 and 747-8. GEnx-1B was meant to power the first flight of the Boeing 787, another variant of the engine being the Trent 1000 by Rolls-Royce based at Derbie. The other important feature of the GEnx is the Twin-Annular Premixing Swirler (TAPS) combustor whose efficiency at converting fuel to energy cuts polluting constituents. The most ideal conditions would be presence of infinite number of injector points for a very fine atomization but the reality is that engineers are limited by the number of injectors hence there will still be liquid droplets. Again, the fuel goes through the process in very few milliseconds that it can’t be converted to gas in such a short time. This is where TAPS comes in-to enable maximum vaporization to maintain lower temperatures and limit Nitrogen oxides whose generation are an exponential function of temperature(According to Steve Csonka-Technical Director of Advanced Programs and Environmental Strategy at GE Aviation).
About Me
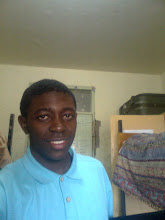
- AICHA EUGENE
- Aicha Eugene is a Mechatronics Engineering student at JKUAT in Kenya. He is also a student member of the SAE.