Labels
Blog Archive
- 2013 (1)
-
2012
(67)
- October(34)
-
September(31)
- September the 30th
- What about internet during our flight?
- September the 29th
- Something is missing….Bird strike kills all!
- September the 28th
- September the 27th
- September the 26th
- September the 25th
- September the 24th
- September the 23rd
- September the 22nd
- September the 21st
- September the 20th
- September the 19th
- September the 18th
- September the 17th
- September the 16th
- September the 15th
- September the 14th
- Top five reasons why Aviation is my way to go
- Effect of wind farms on radar signals
- September the 13th
- The composite fear factor
- Antonov AN-28 crashes at Palana, Russia on 12th Se...
- September the 12th
- Welcome to Avitech Reader!
- September the 11th
- The Airbus Beluga
- B-1 Bomber Targeting pod software for precision
- What is the Airframe
- Diesel engines in Aircraft-what do you think?
- August(2)
The composite fear factor
What are composite materials?
A composite materials is a combination of more than one material put together because each one has a desirable property that we would wish to exploit but we need other properties that are vested in other materials so we join them together and have all the properties we need. Using composite materials also allows the bad property in one material to be ameliorated by the other material that just does better.
If my material science and engineering materials course work serves me right, composites are mainly made up of two components: fibres (fibres to provide tensile strength and flexibility), and a “matrix” to hold the fibres together (providing compressive strength and control of the overall shape).For instance, the “carbon fibre + epoxy resin” combination is widely used in aerospace.
Is it new?
The use of composite materials to build aircraft is not something we can call “A new trend”. It has been around for decades(even before the mid 1980’s) but what we have seen now is a huge increase in the number of parts that are being made with composite materials. In fact in 1988, Airbus introduced the A320 while in 1995, the Boeing Company introduced the Boeing 777-both airplanes in production had all-composite tail sections.Even the DC-9 has parts made of composite materials in it, only that they are few compared to the modern airliners that are being rolled out of factories like the Airbus A350 and the Dreamliner. These aircraft that started offering commercial services after 2011 like the A350 and the Boeing 787 do fly, yes that’s true but being the first generation of aircraft to be mostly composed of parts made of composite materials other than those made of the long safety-trusted metals.this quick transition is something many are deeply questioning despite trusting the work of the engineers and researchers that have worked on it.
The Dreamliner was the first mostly composite aircraft with 50% composite fraction(without the engines) and ferries 210-290 passengers. Next is the Airbus A350, having composite material fraction nearly equal to that in the Boeing 787 but with longer range and higher seating capacity from 250 to 400-plus passengers.
3 – Why did these guys decide to go put in more composite?
Seemingly, we were asleep for all that time only to wake up and find our sleep dream lined….But let us try to understand the truth of the matter because it is not true that long ago, our grand fathers did not realize that composite materials did better. Something imperative to note is that technological breakthroughs in engineering, materials sciences and manufacturing have propagated the notable increase in the use of composites over the past two decades. The use of composite materials has not only invaded aerospace, but also commercial and race car industry, marine industry and the sporting world among many other industries.
Advantages and disadvantages
Composite materials normally result in materials with increased strength, toughness and stiffness. Compared to metals, they have a better strength and stiffness-to-weight ratio. They also boast better corrosion properties and fatigue resistance.This means the planes will last longer and will not require so much maintenance as often. Because of the low weight, there will be lighter aircraft, hence lower fuel consumption and reduced pollution to our environment.
Of course there is no way on earth we will just get all these goodies for free…we must pay something. Setting up a composite production industry is very expensive just say several millions of dollars. Though, over the past decade prices have reduced making composites more accessible and suitable for large-scale aviation projects. Moreover, most manufacturing processes are labor-intensive and high engineering materials knowledge is a necessity. Even the training on composite materials is very expensive making the general manpower package not a very cheap idea to think about.Something else is that we can’t just handle composite materials anyhow….there are handling equipment and specialized storage facilities that are required and this adds more costs, For example, some composites come in “prepreg” form (fibers pre-impregnated with resin) that need frozen storage and have a very limited shelf-life (a few weeks/months).
Then there are issues to do with the safety of workers and staff handling the composites. Several composite material components are classified as hazardous because they have related health issues including complications from inhaling fibers and exposure to suspected carcinogens.
Hurdles to jump
Something else often overlooked by many is the process of commercialization. You don’t just wake up and have your way…there is definitely a process to follow.Before a company is authorized to start manufacturing commercial aircraft, there must be certification and safety assurance procedures first. The US Federal Aviation Administration (FAA) and the European Aviation Safety Agency (EASA) are in charge of investigating aircraft safety and delivering the required certification.
For example, before Boeing started manufacturing the Dreamliner, it was not a question of the many orders already in place for the aircraft but first it had to prove its safety standards to the FAA and EASA.
Lets bring in Robotics now
Lets take an example of a company like Airbus that has received so many order for the Airbus A350 or A380, how do we expect it to deliver 12 aircraft per month all with manual labour? To me, it seems impossible. But if we think about it, we can bring in assistance from robots to make it faster. This will ensure the process is very efficient and will run even during the night, tirelessly. This idea of automation, I remember from a certain magazine, came up in the 1970’s but technology had not developed that much hence it was somehow rendered impracticable as it would be so expensive to implement.
However, in the recent past, low-cost robotic arms have been used for a number of manufacturing processesand Robotic Fibre Placement (RFP) heads started to register their presence more frequently in the market. These placement heads can lay composite materials (using different methods depending on the part at hand) either in a mould or directly on to a desired structure (see video).
About Me
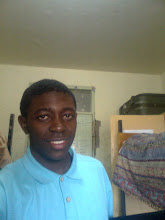
- AICHA EUGENE
- Aicha Eugene is a Mechatronics Engineering student at JKUAT in Kenya. He is also a student member of the SAE.
0 comments:
Post a Comment