Labels
Quality assurance for Composite materials
As an increasing trend, the use of composite materials has faced various challenges. The most underscored challenge that I could point out is that of ensuring quality assurance. A light-weight design of carbon-reinforced plastic (CFRP) utilizes adhesive bonding as the optimum joining technique but quality monitoring procedures are still an issue but once that is circumvented, it will provide a basis for increased use of light weight composite materials for more structures reducing the dominance of rivet based assemblies.
The admirable properties of adhesive bonds are significantly depended on physicochemical behavior of adherend surfaces. This implies there is need for a set of highly advanced NDT techniques to counter check the resulting products of the ENCOMB (Extended Non-Destructive Testing of Composite bonds) project. Adhesive bonding, which we even learnt about in High School, has been established in the Aeronautics industry for more than 20 years. Currently, however, it is mainly used for non load critical parts or components like stiffness panels of vertical tail planes. So, to explore the full potential of this joining technology as applied to other load critical parts like the frame floor modules or fuselage structures, we need adequate Quality assurance procedures. QA procedures for the members that are not load critical are present-conventional NDT to detect defects like pores in the joint areas. As an addendum, the supplied materials (adhesives, prepreg materials) and parameters of the manufacturing processes (like surface treatment and curing) are strictly observed and controlled. It has been established that the overall performance of adhesive bonded CFRP components depends on the intensity of operational loads and the size and density of defects like pores. The adhesion is highly vulnerable to state of the adherend surfaces (for instance degree of contamination and activation after surface pretreatment).
I would also like to bring you to the attention of the two main objectives of the ENCOMB project.One is the development and adaptation of methods of characterization of adherent surfaces before application of adhesive. The second and harder one is the development of techniques for the evaluation of the bonded components resulting from the process. This new approach to testing, referred to as the Extended NDT (ENDT) is based on detection of physicochemical properties that are important for the performance of an adhesive bond. Some ENDT methods are adapted from the spectroscopic methods like IR spectroscopy or Laser Induced Breakdown Spectroscopy (LIBS), and optical methods like laser scanning vibrometry, active thermography and a wetting test. All these help to categorize the state of adherend surfaces. Sensor/fiber based methods like use of embedded optical fiber sensors (EOFS) or electrochemical impedance spectroscopy (EIS) are also suitable for monitoring characteristics of adherend surfaces and adhesives. But mostly for characterization of adhesive bonds, technologies from the field of active thermography using variant excitation sources or optical coherence tomography are applied. Elastic waves techniques like laser excited ultrasonic techniques or nonlinear ultrasonic techniques will also be considered.
Two outstanding contenders
Normally a liquid drop is applied to a surface during the testing and the size of the drop mainly depends on the surface energy and the corresponding contact angle. For the Aerosol Wetting Technique (AWT), small water droplets with a narrow drop size distribution are generated by an ultrasonic atomizer nozzle and sprayed onto the sample surface by a constant airflow. A camera positioned perpendicular to the surface takes a photo of the wetted area. The drop sizes are grouped using software and the mean drop diameter is determined by a two parameter fit to a Rosin-Rammler drop-size distribution. A large mean drop size shows a good wetting property and high surface energy. If the surface energy is low and this is normally caused by surface contaminants like silicones or Teflon, relatively small drops will be formed on the surface hence a small mean drop size. The AWT process is very surface sensitive and can detect surface contaminants (Frekote/Tedlar) on CFRP surfaces and the effects of different plasma treatments that have an influence on the fracture toughness energies of corresponding bonded samples. The accuracy and sensitivity of the measured results can be ameliorated by further statistical analysis, image acquisition and evaluation for droplets on dark and low reflecting CFRP surfaces. The suitableness of the AWT for other scenarios like detection of Skydrol contaminants on CFRP is also something to be looked at.
The Laser Adhesion Test (LASAT)
This method is based on inducing controlled traction by irradiating the target with a high power laser pulse (GW/cm2). The laser energy excites high power plasma (GPa) at the surfaces. Thus, a mechanical shock wave is induced inside the target. The LASAT technique relies on the crossing of two releases that are generating traction. The first release is due to reflection of the incident shock wave at the rear free surface. The second one follows this incident shock wave since the maximum pressure is brought back to the ambient pressure at the end of the load duration. In this way, interface could be damaged if the level of tensile stress exceeds the bond strength and if the shock waves propagation parameters (shock duration and amplitude, materials nature and thicknesses) allow locating the release crossing at the interface. Damage can be assessed by post shock diagnostics (like ultrasonic testing, microscopy) since the shortness of laser impact allows a soft recovery of shocked samples. It can also be done by measurement of rear free surface velocity (velocity interferometric system for any reflector or heterodyne probe). This nonintrusive diagnostic provides clear evidence of the debonding or integrity by very different velocity time histories. Coupled with numerical simulation of shock wave propagation and damage modeling, experiments give a quantitative evaluation of the adhesion threshold of coatings. So use of lase shock waves applied to CFRP bonded samples has shown its ability to differentiate strengths of adhesion. There is more to be learnt on shock wave propagation into CFRPs and adhesives in order to optimize laser parameters to induce a controlled traction at the interface of a given system.
Ref:
Article in SAE Aerospace engineering issue of 15th August 2012
SAE technical paper 2011-01-2514 by Susanne
What is the Airframe
By airframe when it relates to an aircraft we are referring to the mechanical structure of the plane. This includes the fuselage, wings, fin or vertical stabilizer(form the empennage), ailerons and the landing gear. It does not include the electronic system(avionics) or the engines. In aerospace engineering and research, its important to note that the airframe design is a vital elements and combines aerodynamics, manufacturing techniques and material science to achieve its designated purpose or objective. For example, the wings has a certain aerodynamic shape to achieve lift while the landing gear is to be made using specific shock absorbing material and at the same time possess the toughness to withstand impact. The whole airframe has to be robust enough to withstand the stresses it goes through and also balance the safety, reliability and economics. Airframe structures is not something that just came out recently, it can be clearly seen even when you look at the aircraft built by Orville and Wilbur Wright. It has only been advanced and developed over the years to couple its development with technology. I remember during our Aviation Technology classes at Maseno School we learnt about the warren truss structure, the monocoque and the semi-monoloque structures and differentiated between them in details.
The fuselage is also what we know as the main body of the aircraft and provides room for controls, our payload, passengers and the crew.It also provides attachment for wings, the landing gear, the empennage and the powerplant. In the early days, the fuselage was made by welding, riveting or bolting together aluminium tubes and steel rods to form a tapering box like structure whose strength mainly dependent on the weld joints and the strength of the aluminium and steel. The longitudinal members called longerons and the vertical web members had to bear the aerodynamic stresses depending on the direction in which the stresses will be acting. Later on as technology advanced, designs were developed to enclose the truss with a covering, first was cloth which paved way to the light metal sheets like aluminium that ended up bearing most of the flight loads in the monocoque and semi-monocoque construction. The stressed skin provides enough force but if dented or deformed then it can easily give in.It just works like an aluminium can, if it has no dent or deformation, it can be very strong but once it has a hole then it would give in to a substantial amount of force applied.
The true monocoque structure consists of bulkheads, formers and the skin. The formers and bulkheads give shape to the structure. Here, in the monocoque construction , the skin just has to be strong enough to bare all the stresses hence the main challenge is to make it strong without adding its weight so much-a hard compromise. That is why we have the semi-monocoque structure that that has bracing members on which the skin is attached and these bracing members take some of the stresses and its not only left for the skin. This bracing substructure is made up of stringers, variety of sizes of bulkheads and formers to support and ease forces on the stressed skin.
About Me
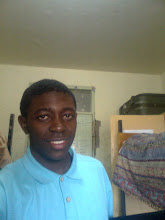
- AICHA EUGENE
- Aicha Eugene is a Mechatronics Engineering student at JKUAT in Kenya. He is also a student member of the SAE.