Labels
New Sensor Could Prolong the Lifespan of High-Temperature Engines
A new, highly-accurate temperature sensor could save manufacturers millions in maintenance costs, lower fuel consumption, and prolong the lifespan of jet engines, nuclear reactors and other types of large gas turbine engines.
A temperature sensor developed by researchers at the University of Cambridge could improve the efficiency, control and safety of high-temperature engines. The sensor minimises drift -degradation of the sensor which results in faulty temperature readings and reduces the longevity of engine components.
The new sensor, or thermocouple, has been shown to reduce drift by 80 per cent at temperatures of 1200 degrees Celsius, and by 90 per cent at 1300 degrees Celsius, potentially doubling the lifespan of engine components. The results are published in the September issue of the Journal of Engineering for Gas Turbines and Power.
Generally, the hotter a jet engine burns, the more power it generates, improving fuel efficiency, range and thrust. However, an accurate temperature reading is critical, as when temperatures get too high, the mechanical integrity of engine components could be at risk. A temperature error of just ten degrees can trigger engine failure, which can be a huge blow to aircraft manufacturers, as seen in the 2010 recall of Rolls-Royce's Airbus A380 engines, which caused the company's share price to drop by a massive nine per cent.
Modern jet engines can reach temperatures as high as 1500 degrees, but drift in the nickel-based thermocouples used to measure temperature increases to unacceptable levels at temperatures above 1000 degrees. Therefore, the thermocouple is placed away from the hottest part of the engine, and the maximum temperature is extrapolated from that point.
The inaccuracy resulting from this form of measurement means that the engine temperature, and therefore efficiency, has to be set below maximum in order to leave a safety margin for the survival of engine components. Thermocouples with increased temperature capabilities can be placed closer to the combustion chamber, increasing the accuracy with which the peak temperature is estimated, and decreasing the required safety margin.
"A more stable temperature sensor provides several advantages -- a better estimation of temperature can increase the lifetime of engine components and decrease maintenance costs to manufacturers, without any reduction in safety," said Dr Michele Scervini, a postdoctoral researcher in the Department of Materials Science and Metallurgy, who developed the new thermocouple.
In its simplest form, a thermocouple consists of two bare wires of two different metals joined together at their ends, with a voltmeter incorporated into the circuit. The difference between the two ends of the thermocouple is measured by the voltmeter and used to determine the temperature. This type of thermocouple is not suitable for high-temperature applications as the elements oxidise above 800 degrees, increasing the amount of drift, so thermocouples sheathed in oxidation-resistant materials were introduced in the 1970s. While this configuration addressed the issue of oxidation, the sheath contaminated the wires at temperatures above 1000 degrees, increasing drift.
Scervini, along with Dr Cathie Rae, has developed a thermocouple which both withstands oxidisation and minimises any contamination to the wires from the metallic sheath. The thermocouple is made of an outer wall of a conventional oxidisation-resistant nickel alloy which can withstand high temperatures, and an inner wall of a different, impurity-free nickel alloy which prevents contamination while reducing drift.
Results from tests on a prototype device showed a significant reduction in drift at temperatures of 1200 and 1300 degrees, meaning that a double-walled thermocouple can be used at temperatures well above the current limitation of 1000 degrees.
There are platinum-based thermocouples which can withstand higher temperatures, but their extremely high cost means that they are not widely used. "Nickel is an ideal material for these applications as it is a good compromise between cost and performance, but there is a gap in the market for applications above 1000 degrees," said Scervini. "We believe our device could see widespread usage across a range of industries."
The team are currently commercialising their invention with the assistance of Cambridge Enterprise, the University's commercialisation arm, and have attracted interest from a range of industries. Tests on new prototypes are on-going.
Something is missing….Bird strike kills all!
My euphoria about the engine that could not succumb to bird strikes never stayed that long…really. I had thought we just found an answer to seal away all these gruesome conditions where a bird imagines to be flying into an advanced nest only to end up in double tragedy-deaths and a damaged engine! Anyway, this happened before someone could implement this in a real aircraft.
This happened on 28th September 2012. The Dornier Do-228 owned by Sita Air climbed up the runway from Kathmandu, Nepal headed to Lukla-still in Nepal. It had 3 crew members and 16 tourists on board and was right in the beginning of that first climb up the runway when a bird accidentally flew into the engine and damaged it. As usual, the first course of action is to return to the airport and land but, in this specific case, this did not work as the aircraft descended at a very fast rate and could not make it to the airport. The only other option was to land at the bank of Manohara River, Koteshwor village. However, this again, did not end well as the plane crashed on that river bank and went up in flames completely consuming everybody and everything…so doleful an end.
According to investigations, a bird hit the right hand engine at about 15m above the ground and caused a part of the engine to separate from the engine and disfigure the rudder. This rendred any turn uncordinated hence the move back to the runway uncontrollable as the pilot could no longer maintain ascendancy over the plane for longer.
To view some more information, you can check here. Some of the pictures are displayed here.
Diesel engines in Aircraft-what do you think?
Let us say…we are revisiting this idea, because it is not just out of the woods. This is something that was there many years ago. Let’s take for instance, the late 1930’s when the Junkers built JUMO-the series of 2-stroke diesel engines whose advantage of fuel economy and mechanical efficiency made them very popular. Talking of such a 2-stroke engine, no poppet valves and its junky operating and timing system, no friction losses due to valves –compare this to the 4-stroke engine and you will surely visualize what I am talking about. Again, why fuel? Can you imagine that depending on size and type of aircraft, the largest portion of it is fuel, sometimes can be as high as 50%!
With the 2-stroke diesel engine, it is possible to attain a high power density and fuel efficiency while at the same time enhancing altitude performance. Another salient feature of diesel engines is that it allows a higher boosting level in comparison to spark-ignited(SI) engines whose capabilities are limited by knocking-yet we know that high octane rating fuel like JP4, JP5 and Jet A is now being subject to very strong limitations due to the damage to mother nature. We haven’t exhausted the list of advantages yet; there is the low volatility of diesel compared to other fuels meaning less explosions and fires. It also has better reliability in flight-no mixture control issues, no carburetor icing issues and safe cabin heating due to reduced exposer to carbon monoxide. Let us also not gainsay the fact that the 2-stroke engine cycle has the exemplary ability to maintain a high power density at a very low crankshaft speed, hence can be directly engaged to a propeller shaft even without the reduction gearbox hence cheaper.
These advantages, coupled with the recent developments in the 2-stroke, compression ignition(CI) diesel engine technology make this an auspicious choice for small planes that only need 100-300 hp, at a lower weight than the existing SI engines. This is very pragmatic owing to the trials by AVL in the late 1990’s when they developed a 1-L, 2-stroke turbocharged diesel engine with uniflow scavenging, achieving a brake power of 50kW and a weight less than 80kg. Another proof of possibility is given by Wilksh Airmotive that brought to the experimental aircraft market a 90kW 3-cylinder 2-stroke engine with IDI (indirect injection)-only weighing 100kg.
Generally, we can say that so far, none of the models has reached certification stages as I am writing this article but we are sanguine that more research and trials with several engine configurations will yield expected victory. Some of the selected engine configurations are like the loop and uniflow scavenging type, as opposed to the piston uniflow type.
Research at the University of Modena & Reggio Emilia and Wilksh pointed out that the uniflow type was actually more intricate (would be heavier and more expensive to manufacture) though had flexibility of exhaust timing events via cam-operated valves. On the other hand, though the loop scavenged engine had the trappings of “simple and cheap”, it brought with it symmetrical inlet and exhaust event timing. It also has more to offer in terms of Power-to-Weight ratio, Fuel efficiency, altitude performance and cooling.
For now, at least we leave the rest for research to decide.
This article has been influenced by another article from SAE Aerospace magazine August 2012.
Optimizing engines for greener combustion
Well, its not like green is my favorite color…okay. It may be yours but it’s mother’s favorite. Did I just say mother? I meant Mother Earth! Under the social responsibility of corporate institution, is environmental responsibility and since most use already manufactured products, the buck stops with manufacturers in terms of materials and configurations used in component manufacture. However, the information has to be passed to consumers like airlines to ensure that the maintenance is done well to conserve and improve upon the parameters already included.
We know that Carbon (IV) oxide emissions is a function of the quantity of fuel burned. We need to focus more on the combustor where oxygen and fuel are mixed and burned if we have to reduce the noxious emissions that remain close to the ground like NOX, uncombusted hydrocarbons, particulate emissions and aerosols and smoke . To address this, we have to look at injectors, swirlers and atomization of fuel. NASA’s Glenn Research Center has been at the forefront of work on improving injector combustion efficiency. At this center, engineers have been trying several injector configurations and air –mixing methods and have developed the Lean Direct Multi-point Injection (LDMPI).
Among the burning goals has been how to put maximum numbers of injectors in minimum areas to improve combustion-the more completely combusted the fuel, the less the emissions. Multi-point refers to the many different entry points of fuel into the combustor. Regulatory agencies like ICAO have set up stringent rules and standards for pollution that have to be met.
NASA has also gone ahead to burn three different types of fuel in LDMPI testing including two Fischer-Tropsch(F-T) and one biofuel. Although they didn’t really significantly change emission quantities, they solved the issue of clogging in combustors due to tinier injector tips as kerosene is burned. The tests were done at NASA’s Dryden Aircraft Facility and used DC-8 engines both main and auxiliary Power units.
Still, under Environmentally Responsible Aviation(ERA) program, there is a need to reduce cooling air necessary to regulate temperature of metallic combustion liner that can easily melt it if not for the cooling breeze. But then, the less air used for this cooling, the more we can utilize in combustion.
GE Aviation is using the lean/burn combustion to run the GEnx engine that powers the 787 and 747-8. GEnx-1B was meant to power the first flight of the Boeing 787, another variant of the engine being the Trent 1000 by Rolls-Royce based at Derbie. The other important feature of the GEnx is the Twin-Annular Premixing Swirler (TAPS) combustor whose efficiency at converting fuel to energy cuts polluting constituents. The most ideal conditions would be presence of infinite number of injector points for a very fine atomization but the reality is that engineers are limited by the number of injectors hence there will still be liquid droplets. Again, the fuel goes through the process in very few milliseconds that it can’t be converted to gas in such a short time. This is where TAPS comes in-to enable maximum vaporization to maintain lower temperatures and limit Nitrogen oxides whose generation are an exponential function of temperature(According to Steve Csonka-Technical Director of Advanced Programs and Environmental Strategy at GE Aviation).
About Me
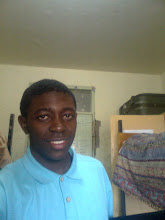
- AICHA EUGENE
- Aicha Eugene is a Mechatronics Engineering student at JKUAT in Kenya. He is also a student member of the SAE.